The Duty of Welding Examination in Preventing Failures and Enhancing the Longevity of Welded Structures and Components
Welding evaluation is a necessary part in the lifecycle of bonded frameworks, functioning as a positive action versus possible failings that can jeopardize security and functionality. By systematically recognizing issues such as porosity or insufficient blend, assessors can significantly boost the long life of important parts. The application of diverse inspection strategies not just makes sure compliance with market standards yet additionally cultivates a robust society of quality guarantee. Nonetheless, the ramifications of neglecting this essential method can be profound, questioning about truth effect on structural honesty and long-lasting performance. What are the finest methods that can further elevate assessment effectiveness?
Significance of Welding Examination
Welding evaluation functions as a critical protect in the honesty of welded structures, making certain that they meet strict security and top quality standards. The significance of this procedure can not be overemphasized, as it plays a vital role in determining possible concerns before they escalate into disastrous failings. By carefully reviewing welds, inspectors can verify adherence to develop requirements and governing requirements, thereby reducing dangers linked with architectural concession.
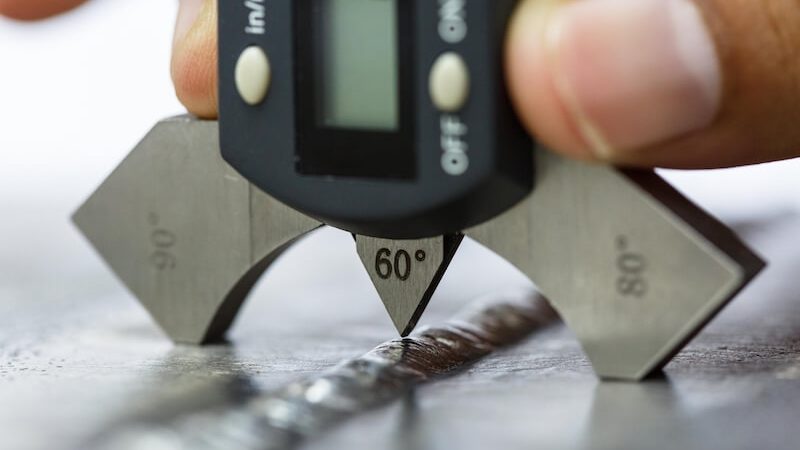
Additionally, reliable welding examination enhances the longevity of elements, as it enables the early discovery of defects that might cause damage with time. This proactive approach not just expands the solution life of welded structures however also advertises dependability and operational performance. In markets such as building, aerospace, and automobile, where safety and security is extremely important, the assessment process is essential.
Furthermore, welding examination promotes a culture of quality control within organizations, encouraging adherence to ideal methods and constant enhancement. By investing in comprehensive inspection procedures, business can improve their credibilities and keep customer trust fund. Eventually, the relevance of welding assessment hinges on its capability to copyright security, quality, and durability in bonded structures, making it a basic component of design integrity.
Typical Welding Defects
A number of common welding problems can endanger the honesty of welded structures, bring about prospective failings otherwise attended to. Among these issues, porosity is one of the most widespread, defined by the presence of small gas pockets caught within the weld steel. This can considerably damage the joint, resulting in decreased architectural integrity.
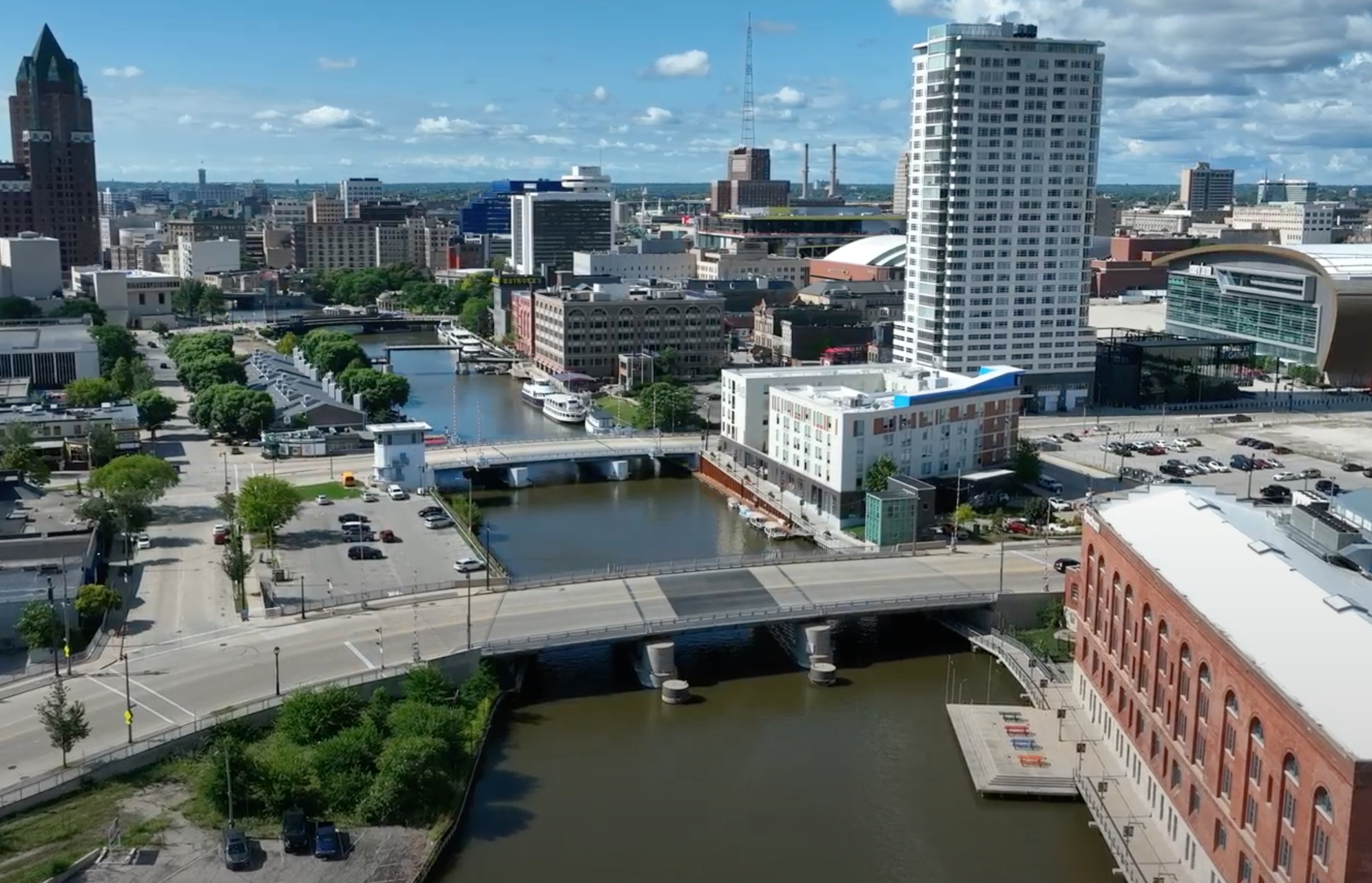
An additional defect is incomplete combination, which happens when the weld steel fails to effectively fuse with the base product or previous weld layers. This absence of bonding can develop weak factors that might stop working under stress and anxiety. In a similar way, absence of infiltration describes inadequate depth of weld metal, stopping the joint from accomplishing its designated stamina.
Splits can likewise establish during the welding process, frequently due to rapid air conditioning or inappropriate welding criteria. These splits may propagate under lots, bring about disastrous failures. Additionally, too much spatter can prevent the weld's quality by presenting pollutants.
Assessment Methods and Methods
Efficient inspection strategies and techniques are critical for guaranteeing the honesty and durability of welded frameworks. An extensive inspection routine employs a variety of non-destructive testing (NDT) approaches to find prospective issues without jeopardizing the bonded elements. Amongst the most frequently used methods are visual assessment, ultrasonic testing, radiographic testing, magnetic fragment testing, and color penetrant testing.
Visual examination functions as the initial line of defense, enabling inspectors to determine surface area problems such as splits, misalignments, or insufficient fusion. Ultrasonic testing utilizes high-frequency acoustic waves to detect interior imperfections, providing in-depth information regarding the product's honesty. Radiographic testing utilizes X-rays or gamma rays to envision the internal structure of welds, making it possible for the identification of incorporations and voids.
Magnetic bit screening works for detecting surface area and near-surface suspensions in ferromagnetic products, while color penetrant testing highlights surface-breaking flaws using colored dyes. Each approach has its distinct benefits and limitations, necessitating a calculated mix to attain thorough inspection protection. Applying these methods methodically makes certain that published here any potential issues are recognized early, cultivating the dependability and toughness of bonded frameworks.
Effect On Architectural Stability
The stability of a structure is considerably influenced by the quality of its welded joints, as they work as essential factors of toughness and stability. Improperly carried out welds can result in tension concentrations, exhaustion failures, and eventually, devastating structural collapse. The dependence on welding as a main ways of joining products requires rigorous inspection methods to make sure that welds meet established criteria and specs.
Deficiencies in weld top quality, such as insufficient fusion, splits, or porosity, can jeopardize the mechanical buildings of the joint, impacting load-bearing capacity and total performance. When these defects go unseen, they can propagate under functional anxieties, resulting in a decline in structural integrity gradually. Complete and normal inspections are crucial in identifying these weak points before they intensify right into considerable failings.
Moreover, the effect of environmental elements, such as deterioration, can be intensified by poor welding practices. Therefore, making certain premium welding via alert examination not only promotes prompt architectural reliability however additionally extends the solution life of parts. Welding Inspection Milwaukee. Ultimately, the investment in appropriate welding examination is a necessary approach for protecting against architectural failings, thereby improving the long life and safety of welded structures
Best Practices for Effective Assessment
Carrying out organized examination methods is essential for guaranteeing the integrity of welded joints. Efficient examination starts with the growth of extensive lists customized to the details welding procedures and products included. These checklists ought to encompass visual inspections, non-destructive testing (NDT) methods, and documents testimonial to make certain that all elements of the welding procedure are inspected.
Training and certification of examination personnel are crucial elements of an effective inspection program. Inspectors need to be skilled in various NDT strategies, consisting of ultrasonic, radiographic, and magnetic bit testing, to properly determine problems such as cracks, porosity, and insufficient combination.
Prompt examinations must be scheduled at numerous phases of the welding process-- pre-weld, during welding, and post-weld-- to capture any type of potential concerns early. Additionally, keeping in-depth records of examinations promotes accountability and promotes future examinations.
Conclusion
Welding examination is necessary for recognizing flaws and guaranteeing the honesty of welded frameworks. By employing numerous inspection strategies, potential problems can be detected early, consequently preventing disastrous failures and improving the long life of components. The application of ideal practices in assessment fosters a culture of top quality assurance, guaranteeing conformity with design specs and governing standards. Eventually, efficient welding examination not just safeguards architectural honesty yet likewise adds significantly to the total reliability and durability of welded joints.
Welding examination is an essential component in the lifecycle of bonded frameworks, offering as a positive step against possible failings that can jeopardize security and functionality.Welding inspection offers as helpful site an important secure Continued in the stability of welded frameworks, making sure that they fulfill strict safety and top quality requirements. Welding Inspection Milwaukee. Ultimately, the significance of welding evaluation exists in its capability to support security, quality, and longevity in bonded structures, making it a fundamental element of engineering honesty
Eventually, the investment in correct welding evaluation is an important strategy for securing against architectural failures, therefore improving the long life and security of bonded structures.
Welding examination is essential for determining flaws and guaranteeing the honesty of welded frameworks. Welding Inspection Milwaukee.
Comments on “What to Anticipate from a Comprehensive Welding Inspection Milwaukee Process”